A Swiss electric guitar from A to Z
Building an electric guitar requires carpentry, mechanics and electronics. Many manufacturers buy prefabricated parts. The Duvoisin company in Neuchâtel does everything itself.
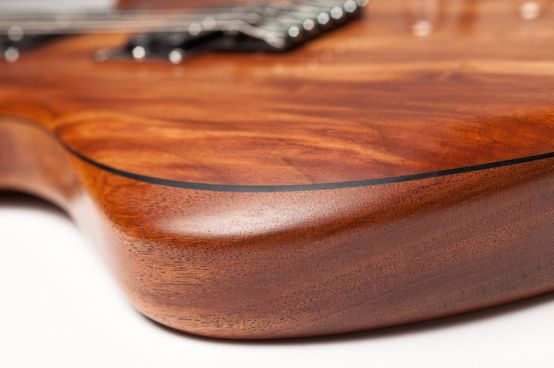

Building an electric guitar requires carpentry, mechanics and electronics. Many manufacturers buy prefabricated parts. The Duvoisin company in Neuchâtel does everything itself.
One day, Jacques Duvoisin, a watchmaker and restorer, hears the sound of an electric bass on the street. He decides to switch to developing and manufacturing electric guitars and basses. His guitar-loving son Gilles graduated from business school and then turned to the instrument trade. Because even a passion does not come without the right training, he completed a three-month internship at Warrior Instruments in Rossville, Georgia, USA. On his return, he opened the ACE Guitars store in Saint-Blaise. For the woodworking, father and son Duvoisin brought in Didier Coulet, whose family ran a sawmill in the area. After numerous experiments and a lot of tinkering, they develop a range of electric guitars and basses: the "Swiss Sonic Signature", which they launch on the market in 2008.
- Gilles Duvoisin fine-tuning an electric guitar.
Watchmaker, instrument maker, engineer and banker
Today, Duvoisin employs four people who complement each other perfectly with their professional skills. Jacques Duvoisin takes care of the technical organization, the plans and the mechanical research. He contributes ideas and tests new technologies together with the electrical engineer. Gille's areas of responsibility are the fine adjustment of manufactured instruments, instrument construction in the narrower sense and repairs of instruments of all brands. He serves and advises customers, demonstrates the instruments and responds to personal requests. Gérald Huguenin is a full-time professor at the HE-Arc engineering school. He is responsible for the research and development of electronic components. The fourth member of the team, Pierre Camilleri, is a lawyer with a background in banking. He ordered three basses from Duvoisin and then took a closer interest in the company. Today, he is responsible for finance, communication and marketing.
In-house technical developments
The four are in search of a unique product. They try to introduce improvements at every stage of production: in the shape, the wood, the design, the mechanics and the electronics. At the moment, their range consists of three instrument series: With the "Standard", Duvoisin distinguishes itself from the big brands Gibson, Fender, Ibanez, Yamaha. The "Super Standards" for guitars or "Fat Standards" for basses are instruments for fans who are dedicated to music and are looking for an instrument to accompany them every day. The "Custom" range consists of custom-made instruments according to the customer's wishes.
Unlike many other instrument makers, the Duvoisin company manufactures the pickup itself; the most important innovations can be found around the microphones. With the Duvoisin MIG-82 humbucker, they have designed a pickup whose magnetic plates can be inserted or replaced without having to replace the microphone as a whole. An active pickup was developed for electric basses, which greatly enhances the sound quality and preserves the transparency of the different types of wood used. A patented bridge plate and strings without brass balls are further innovations on the way to an ever better sound.
The Duvoisin recently presented their instruments at the NAMM in Anaheim/California, the world's largest professional music trade fair. They discovered that they are practically the only instrument makers who make their own microphones. A young Japanese professional musician was moved to tears after playing a custom bass made of poplar wood.